Prüfung des Nockenwellensensors
Die Überprüfung des Nockenwellenpositionssensors ermöglicht es, seine Funktionsfähigkeit und korrekte Funktion zu überprüfen. Anhand der Symptome einer Fehlfunktion kann man den Totalausfall des Sensors oder seinen instabilen Betrieb erkennen, und für eine genaue Diagnose benötigt man ein Multimeter oder einen Diagnosescanner. In der Regel fällt der Sensor selbst selten aus, aber seine Verkabelung und sein Stecker erfordern Aufmerksamkeit.
Lage des Nockenwellensensors am Motor
Um den Nockenwellenpositionssensor zu prüfen, müssen Sie wissen, wo er sich befindet. Bei Achtventil-Motoren ist der Nockenwellenstellungssensor in der Regel am Ende des Zylinderkopfs angebracht. Bei 16-Ventil-Motoren ist er ebenfalls am Zylinderkopf angebracht, meist in der Nähe des ersten Zylinders.
Anzeichen für einen defekten Nockenwellenstellungssensor
Wenn der Nockenwellensensor ausfällt (das elektronische Steuergerät empfängt falsche oder gar keine Informationen von ihm), ist der Wechsel in den Notbetrieb programmiert. Dies bedeutet, dass der Motor mit einer paarweise-parallelen (Gruppen-) Kraftstoffzufuhr versorgt wird. Dies führt zu zwei negativen Folgen:
- Leichter Leistungsverlust des Motors, insbesondere bei kritischen Fahrzuständen (Beschleunigung, Fahren unter Last).
- Anstieg des Kraftstoffverbrauchs um etwa 10...20 % (abhängig von der Motorleistung, den Konstruktionsmerkmalen und den Betriebsbedingungen).
Bei Dieselmotoren sind die Sensoren für die Nockenwellenposition ähnlich angeordnet, aber es gibt einen Unterschied. Er besteht darin, dass der Sensor nicht nur die Position des ersten Zylinders, sondern aller Zylinder feststellt. Dies wird dadurch erreicht, dass es für jeden Zylinder einen eigenen Zahn auf der Zielscheibe gibt.
Sie können den Ausfall des Sensors also daran erkennen, dass sich die Funktionsweise des Fahrzeugmotors ändert, und auch an einigen anderen Symptomen.

4 Anzeichen für einen defekten Nockenwellenpositionssensor oder fehlerhafte Symptomcodes: video
- Beim Anlassen des Motors muss der Anlasser länger gedreht werden.
- Instabiler Betrieb des Motors, Motor Drehzahlschwankung und Leerlaufdrehzahlen des Motors.
- «Einbrüche» in der Fahrzeugbewegung, wenn man das Gaspedal betätigt, reagiert es nicht sofort, die dynamischen Eigenschaften des Fahrzeugs gehen verloren (beschleunigt schwach, zieht nicht, vor allem im beladenen Zustand und beim Bergauffahren).
- Beim Zurücksetzen des Gaspedals wird der Motor abgewürgt.
- Der Kraftstoffverbrauch ist erhöht (um 10...20%).
- Die Signallampe Check Engine auf dem Armaturenbrett wird aktiviert. Typische Fehlercodes (wenn sie mit dem Scanner diagnostiziert werden), die die Arbeit des Sensors betreffen, haben die Nummern P0340, P0342, P0343.
Wie prüft man den Nockenwellensensor?
Bevor Sie den Sensor mit einem Multimeter oder anderen elektronischen Geräten überprüfen, müssen Sie ihn visuell überprüfen. Das heißt, die Unversehrtheit des Sensorgehäuses, das Vorhandensein von Rissen oder anderen Schäden. Es ist auch wünschenswert, die Führungsscheibe auf beschädigte Zähne und auf Metallspäne auf oder in der Nähe des Sensorgehäuses zu überprüfen.
Es gibt zwei grundsätzliche Möglichkeiten, den Nockenwellensensor zu überprüfen — mit einem elektronischen Multimeter und mit einem Oszilloskop. Die erste Methode ist einfacher und schneller, aber die zweite ist genauer und liefert mehr Diagnoseinformationen. Es lohnt sich jedoch nicht, mit einem Metallgegenstand auf das Vorhandensein magnetischer Eigenschaften zu prüfen, da ein nicht funktionierender Nockenwellenstellungssensor ebenso magnetisch sein kann wie ein funktionsfähiger.
Wie prüft man einen Nockenwellenpositionssensor mit einem Multimeter?
Zum Testen muss die Spannung eines Nockenwellenstellungssensors gemessen werden, die an seiner Signalleitung erzeugt wird. Die Daten, die Sie erhalten, hängen vom Sensortyp und dem Fahrzeugmodell ab. Beachten Sie auch, dass der Sensor je nach Typ eine unterschiedliche Anzahl von Stiften hat. Ein magnetischer oder induktiver Sensor hat zwei Drähte, ein Hall-Effekt-Nockenwellensensor hat drei Drähte. Sie sollten auch den Durchgang der Drähte überprüfen. Für die Diagnose benötigen Sie ein Multimeter im Gleichstrom- und Wechselstrommodus (für Doppelstifte).
Bevor Sie mit dem Test beginnen, sollten Sie die Box in den Leerlauf (bei Schaltgetriebe) oder in die Parkstellung (bei Automatikgetriebe) schalten, die Feststellbremse anziehen und außerdem das Kraftstoffsystem abklemmen, indem Sie die Überbrückung der Kraftstoffpumpe vom Sicherungsblock abziehen, um ein Anlassen des Motors zu verhindern. Finden Sie dann heraus, welcher Sensorstift für was verantwortlich ist.
Prüfung des Nockenwellensensors mit 3 Kabeln
Prüfung des Nockenwellensensors mit 3 Kabeln
- Stellen Sie den Gleichspannungsmodus am Multimeter ein und ziehen Sie den Sensorstecker ab;
- Schließen Sie den roten Messfühler an das Stromkabel und den schwarzen Messfühler an den Minuspol der Batterie an;
- Bitten Sie Ihren Partner, den Motor ein paar Sekunden lang zu starten;
- Der Spannungswert auf dem Messgerät sollte etwa 5 Volt betragen (so können Sie sowohl die Unversehrtheit des Stromkabels feststellen als auch, ob es mit Strom versorgt wird);
- Um festzustellen, ob das Minuskabel des Sensoranschlusses intakt und kurzgeschlossen ist, schließen Sie den roten Messstab daran an und lassen Sie den schwarzen am Minuspol der Batterie;
- Bitten Sie Ihren Helfer, den Motor erneut anzulassen, und schauen Sie dabei auf den Bildschirm des Multimeters. Der Spannungswert sollte 0,1 oder 0,2 V betragen;
- Wiederholen Sie den gleichen Vorgang nur mit dem Signalkabel, nur dass dieses Mal die Spannung auf dem Display zwischen 0 und 5 Volt schwanken sollte (wenn es gut ist);
- ohne den Motor zu starten, aber nur bei eingeschalteter Zündung, die Spannung zwischen dem Plus- und dem Signalkontakt messen. Sie muss mindestens 90 % der Versorgungsspannung betragen.
Prüfen eines 2-Draht-Nockenwellensensors
Prüfen Sie nacheinander, ob die Drähte intakt sind und ob der Stecker funktioniert. Um den induktiven Typ (meist in älteren Fahrzeugen eingebaut) zu prüfen, verwenden Sie mehrere Methoden: Prüfen Sie, ob während des Betriebs Spannung an der Signalleitung anliegt und ob der Sensor ein eigenes Wechselstromsignal erzeugt.
Um die Stromversorgung des Kurbelwellensensors vom magnetischen Typ zu überprüfen, ist es notwendig:
Prüfen eines 2-Draht-Nockenwellensensors
- den Stecker vom Nockenwellenpositionssensor abziehen;
- das Multimeter auf 20V Gleichspannung einstellen;
- die Zündung einschalten (aber den Motor nicht starten);
- die rote Sonde des Digitalmultimeters an die Signalleitung (in der Regel blau) und die schwarze an den Minuspol der Batterie anschließen;
- Das Signal, das das Digitalmultimeter auf dem Display anzeigt, sollte nahe bei 1,5 V liegen (der genaue Wert ist jedoch nur im Reparaturhandbuch des jeweiligen Fahrzeugs zu finden).
- Um zu prüfen, ob das Massekabel unterbrochen ist, stellen Sie den Schalter des Multimeters auf den Testmodus;
- Schließen Sie den roten Messfühler des Multimeters an die zweite Klemme des Chips und den schwarzen Messfühler an den Minuspol der Batterie an — ein Piepton zeigt an, dass die Verkabelung intakt ist.
- Stellen Sie das DMM in den Wechselspannungsmodus;
- Schließen Sie die Messfühler an die Leitungen des Sensors an;
- Starten Sie den Motor für einige Sekunden (bitten Sie um Hilfe), um zu sehen, ob das Multimeter irgendwelche Messwerte anzeigt.
Wenn der Sensor ausgebaut ist, können Sie einen weiteren Test im Wechselspannungsmodus durchführen. Bringen Sie einen Metallgegenstand an das Ende des Sensors (seinen Signalteil). Messen Sie erneut die Spannung am Signalkontakt. Sie sollte nicht mehr als 0,4 V betragen. Wenn die Platte entfernt wird, sollte die Spannung wieder 90...100% der Versorgungsspannung betragen.
Treten bei der Prüfung Abweichungen auf, bedeutet dies, dass der Sensor defekt ist und ausgetauscht werden muss.
Neben der Spannung des Nockenwellenpositionssensor vom magnetischen Typ kann auch der Widerstand seiner Spule geprüft werden. Stellen Sie dazu das Multimeter auf den Ohm-Modus ein und messen Sie den Widerstand an den Stiften des Sensors (Sie brauchen ihn nicht zu demontieren). Bei einigen Modellen muss der Widerstandswert im Bereich von 200 — 900 Ohm liegen (der genaue Wert ist im Handbuch oder in den technischen Daten des Sensors angegeben). Wichtig ist, dass der Widerstand nicht gegen unendlich tendiert, so dass er auf einen Bruch der Wicklung hinweist und auf jeden Fall ausgetauscht werden muss.
Überprüfen des Nockenwellenpositionssensor mit einem Oszilloskop
Überprüfung des CMP-Sensors mit einem Oszilloskop
Ein elektronisches Oszilloskop hilft zu verstehen, wie der Nockenwellenstellungssensor funktioniert und ob er Impulse erzeugt. Es gibt sowohl spezielle Diagnosegeräte als auch Simulatoren, bei denen es sich um Laptop- oder Smartphone-Programme handelt, und die Verbindung wird hergestellt, indem der Diagnosescanner an den OBD-2-Anschluss angeschlossen wird.
Das Oszillogramm des Nockenwellensensors sollte ein gleichmäßiges Diagramm mit einer ausfallenden Spitze sein, die dem Durchgang des Klopfers durch den Sensor entspricht. Wenn Sie also den Magnetsensor überprüfen, sollte eine Sinuskurve vorliegen, und wenn Sie den Sensor mit Hall-Effekt überprüfen, wird das digitale Signal quadratisch sein und die Punkte mit der höchsten und niedrigsten Spannung aufweisen. Wenn es eine andere Form hat, ist eine zusätzliche Prüfung erforderlich.
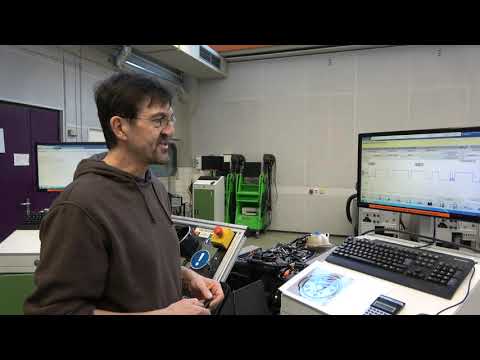
BS16 LF7 Nockenwellensensor mit Hallgeber: video
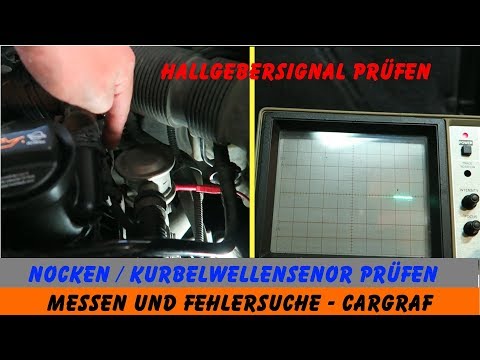
Nockenwellen — Sensor prüfen — Oszilloskop: video
Bei der Diagnose des Nockenwellensensors von «Nissan»-Autos (insbesondere Nissan Almera) mit einem Oszilloskop wird die Form des Oszillogramms anders sein. Es wird nicht flach sein, sondern in Form von 3 Impulsen, dann eine Lücke, dann 4 Impulse — eine Lücke, 2 Impulse — eine Lücke und ein Impuls — eine Lücke. Diese Besonderheit ist die Norm für die Motoren dieses Automobilherstellers.